相關(guān)內(nèi)容
-
一文了解硬質(zhì)合金相關(guān)術(shù)語
1.硬質(zhì)合金指由難熔金屬碳化物和金屬粘合劑組成的燒結(jié)復(fù)合材料,在目前所使用的金屬碳化物中,碳化鎢(WC),碳化鈦(TiC),碳化鉭(TaC)和碳化鈮(NbC)是最常見的成分。鈷金屬作為粘結(jié)劑,廣泛應(yīng)用于硬質(zhì)合金生產(chǎn)中;其它的金屬粘結(jié)劑也可應(yīng)用,如:鎳(Ni),鐵(Fe)等,針對某些的特殊用途,也被采用。
-
高頻疲勞測試,不是所有的金屬材料都適合,為什么?
金屬材料疲勞試驗(yàn)是指在一定條件下,對金屬材料施加交變載荷或者循環(huán)載荷,以評價其在循環(huán)應(yīng)力下的耐久性和抗疲勞性能。主要有應(yīng)力疲勞和應(yīng)變疲勞,應(yīng)力疲勞通常對應(yīng)高周疲勞,而應(yīng)應(yīng)變疲勞通常對應(yīng)低周疲勞。低周疲勞通常指10的四次方以下的疲勞,高周疲勞通常指10的四次方以上的疲勞,關(guān)于低周疲勞和高周疲勞的界限不是物理上的,是領(lǐng)域內(nèi)的習(xí)慣性或經(jīng)驗(yàn)性定義。金屬材料的疲勞試驗(yàn)的主要目的是確定材料的疲勞極限、疲勞壽命以及疲勞裂紋擴(kuò)展速率,從而幫助預(yù)測材料在長期使用中的壽命和安全性。
-
不同霧化壓力下GH3536 合金粉末制備和氣霧化過程模擬
使用真空感應(yīng)熔煉氣體霧化方法,在不同霧化壓力(7、8、9 MPa)下制備了球形GH3536 合金粉末。通過使用多相流模型和離散相模型對噴嘴下方區(qū)域進(jìn)行了數(shù)值模擬,再現(xiàn)了不同霧化氣壓下的一次霧化和二次霧化過程。實(shí)驗(yàn)和模擬的結(jié)果表明:回流區(qū)的氣體速度和滯止壓力隨霧化氣壓的提高而增加,霧化氣壓的增加使粉末粒度不斷減小,模擬結(jié)果與實(shí)驗(yàn)結(jié)果吻合,驗(yàn)證了霧化模型的可靠性。提高霧化氣壓可提高細(xì)粉收得率,但顆粒尺寸的減小和顆粒形貌的改變會對粉末的流動性能造成直接影響,在霧化壓力8 MPa 下制備的粉末具有最佳的流動性和松裝密度,分別為14.34 (s·50g-1)和4.728 g·cm-3。
-
金屬粉末是什么,有什么用
金屬粉末是一組可以通過還原、熱解、電解等方法制備的相對較小的金屬顆粒。
淺談硬質(zhì)合金的增材制造
目前 3D 打印的材料范圍主要包括有機(jī)高分子材料(塑料、樹脂、橡膠等)、金屬材料(鎳基高溫合金、鈦合金、鎂鋁合金、不銹鋼、貴金屬等)、陶瓷材料(氧化鋁-氧化鋯共熔體)等等,3D 打印對于硬質(zhì)合金材料的研究和產(chǎn)業(yè)化遠(yuǎn)遠(yuǎn)落后于其他材料。
硬質(zhì)合金是一種復(fù)合材料,通常包括難熔金屬碳化物(鈦、鉬、鎢、鉭、鈮等的碳化物)和粘結(jié)金屬(鎳、鉬、鎢、鈷等),通過粉末冶金等方式燒結(jié)而成。硬質(zhì)合金具備優(yōu)良的力學(xué)性能,有良好的耐磨性能、抗氧化性以及熱穩(wěn)定性,廣泛應(yīng)用于金屬切割和成形應(yīng)用,磨料漿噴嘴、機(jī)械密封圈和軸承,石油鉆井等方面,被譽(yù)為“工業(yè)的牙齒”。
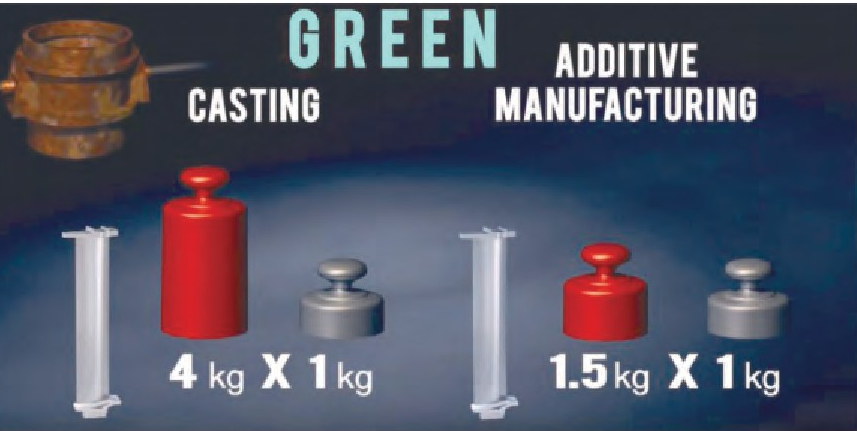
硬質(zhì)合金一般通過傳統(tǒng)手段如注射成型、擠壓成型、模壓成型、熱壓、熱等靜壓、火花等離子燒結(jié)等方式制備。此外,等離子噴涂、反應(yīng)火焰噴涂、鎢惰性氣體(TIG)電弧熔化和激光表面處理等表面改性方法已被應(yīng)用于硬質(zhì)合金包覆材料和涂層的制備。
當(dāng)前硬質(zhì)合金制備技術(shù)仍然面臨一些嚴(yán)峻的技術(shù)挑戰(zhàn),這主要包括:
硬質(zhì)合金產(chǎn)品制備完全依賴模具,而模具成本高、周期長、后續(xù)加工成本高(很多時候占成本 50%以上),對硬質(zhì)合金制造成本造成很大影響;
很多復(fù)雜形狀硬質(zhì)合金制品無法采用常規(guī)及先進(jìn)粉末冶金方法制備,例如中空件、內(nèi)孔、內(nèi)凹槽、小角度彎角、刀具的斷屑槽等,嚴(yán)重限制了硬質(zhì)合金制品的結(jié)構(gòu)設(shè)計(jì)空間;
傳統(tǒng)硬質(zhì)合金制備技術(shù)無法實(shí)現(xiàn)多功能/變化功能復(fù)合結(jié)構(gòu)、梯度結(jié)構(gòu)硬質(zhì)合金的制備,明顯阻礙了硬質(zhì)合金的應(yīng)用領(lǐng)域拓展和優(yōu)勢發(fā)揮。
增材制造(AM)是一種顛覆性的技術(shù),可以根據(jù)設(shè)計(jì)的 CAD 文件逐層累積材料形成復(fù)雜形狀的零件。增材制造技術(shù)能夠輕易實(shí)現(xiàn)復(fù)雜幾何形狀零件的生產(chǎn)制備,有望在硬質(zhì)合金的生產(chǎn)應(yīng)用上降低生產(chǎn)成本。因此,硬質(zhì)合金的增材制造越來越受到人們的重視。
對于金屬增材制造技術(shù)而言,主要的技術(shù)手段包括粉末床融合(PBF),如激光選區(qū)熔化(SLM)和電子束增材制造(EBM);直接能量沉積(DED),如激光近凈成型(LENS)和電弧增材制造(WAAM)。由于硬質(zhì)合金極高的熔點(diǎn),使用增材制造技術(shù)仍然具有很大的挑戰(zhàn)性。
目前,已經(jīng)使用于硬質(zhì)合金的增材制造技術(shù)主要包括:激光選區(qū)熔化(SLM)、激 光 選 區(qū) 燒 結(jié)(SLS)、激 光 近 凈 成 型(LENS)、粘接劑噴射 3D 打?。?DP)、3D 凝膠打?。?DGP)。增材制造技術(shù)能夠成功制備接近理論密度、力學(xué)性能良好的硬質(zhì)合金零件,但也存在許多的問題。裂紋、孔洞、表面粗糙等是增材制造硬質(zhì)合金中不可避免的質(zhì)量缺陷,而且增材制造本身的重復(fù)加熱冷卻過程會形成獨(dú)有的微觀組織,影響零件性能。而通過熱等靜壓和熱處理等后處理手段又會帶來額外的時間和成本,阻礙了增材制造硬質(zhì)合金的發(fā)展進(jìn)程。
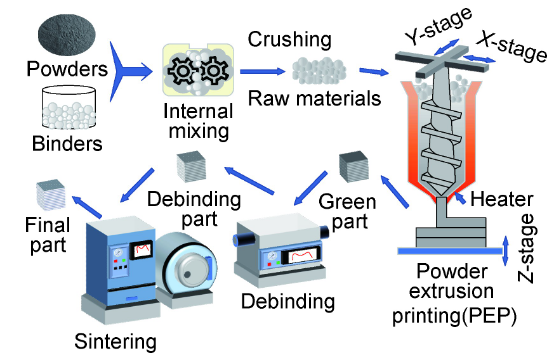
選擇性激光燒結(jié)(SLS)是快速成型(RP)技術(shù)之一,分別為間接激光燒結(jié)(EMLS)和直接激光燒結(jié)(DMLS)。它可以直接以金屬粉末制造任意形狀的三維(3D)零件,適用于硬質(zhì)合金進(jìn)行小批量制造。
硬質(zhì)合金的 SLS 成形技術(shù)往往需要后續(xù)處理,如元素熔滲提高綜合性能。通過添加稀土氧化物作為形核位點(diǎn)細(xì)化晶粒能夠提高零件的相對密度和微觀硬度。
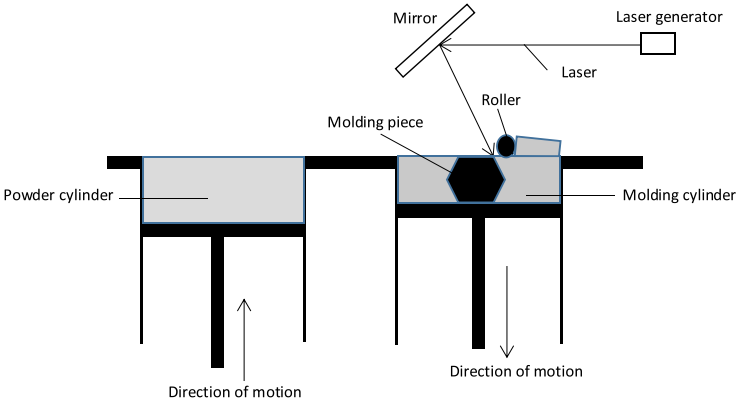
硬質(zhì)合金的 LENS 成形技術(shù)中,提高激光功率密度和進(jìn)粉速度能夠得到更高的樣品高度,提高成形質(zhì)量。LENS 制備的合金在高度方向上存在力學(xué)性能的不一致性,其建造方向與 SLM 類似,存在層狀組織。
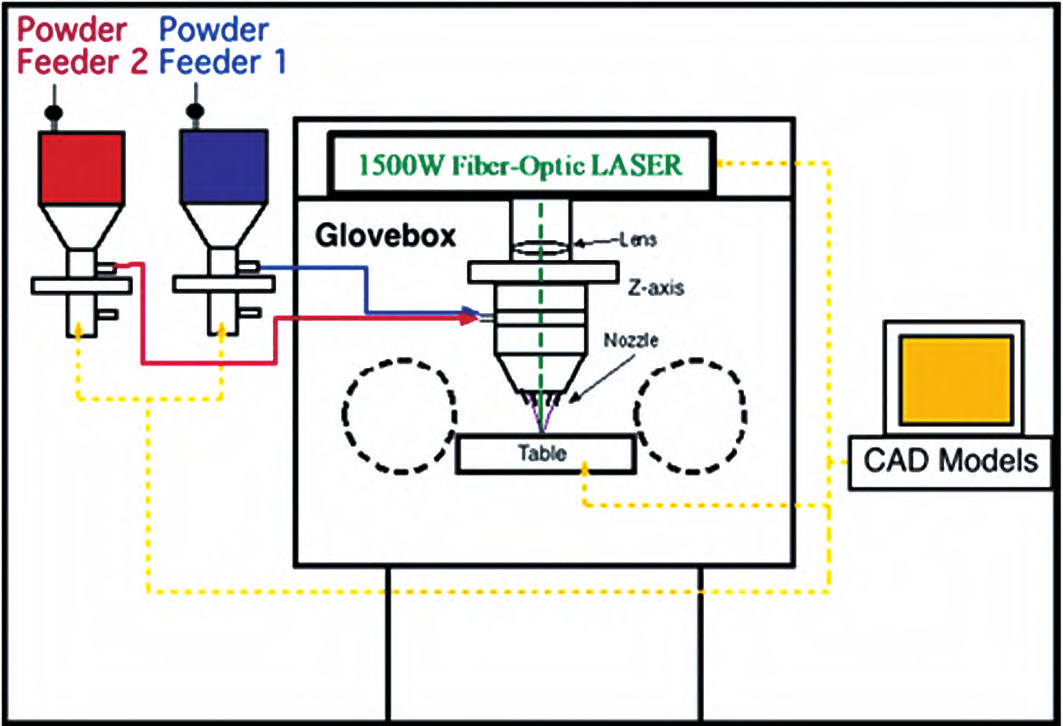
硬質(zhì)合金的3DP成形技術(shù)工作溫度較低,避免了元素蒸發(fā),顯微組織均勻,耐磨性更好。通過使用粘結(jié)金屬(鎳、鉬、鎢、鈷等)作為金屬粘合劑后處理滲透,能夠得到與傳統(tǒng)硬質(zhì)合金相媲美的零件。
硬質(zhì)合金的 3DGP 成形技術(shù)零件一般不存在明顯的裂紋和孔洞缺陷,組織整體分布均勻,力學(xué)性能優(yōu)良。
激光選區(qū)熔化(SLM)技術(shù)是利用高能激光將金屬粉末完全熔化,經(jīng)快速冷卻凝固成型。與 SLM 打印金屬材料相比,硬質(zhì)合金的 SLM 打印難度要大得多,致密化機(jī)理也更為復(fù)雜,其根本原因在于 SLM 打印工藝過程中只有 Co 粘接相能夠熔化,WC 陶瓷相由于熔點(diǎn)非常高(大于 2700℃),在打印過程中不會熔化并嚴(yán)重阻礙硬質(zhì)合金的致密化進(jìn)程。
硬質(zhì)合金的 SLM 成形技術(shù)易產(chǎn)生裂紋孔洞缺陷,通過適當(dāng)增加 WC-Co合金中 Co含量可以避免脆性相的產(chǎn)生,減小裂紋敏感性。通過工藝可以調(diào)控合金的微觀組織?;谶@些特征,可以通過調(diào)整能量密度來獲得不同的微觀組織結(jié)構(gòu)。對于硬質(zhì)合金,高能密度產(chǎn)生的是 WC晶粒小、Co含量低的脆性組織;低能量密度產(chǎn)生的是 WC 晶粒大、Co 含量高的韌性組織。通過工藝調(diào)控組織是 SLM 制備零件的重要手段,然而目前仍缺乏進(jìn)一步的研究。
SLM 目前難以生產(chǎn)近乎理論密度的硬質(zhì)合金零件,需要進(jìn)一步研究工藝與零件成形質(zhì)量和組織之間的關(guān)系;3DP 和 3DGP 相比 SLM 能夠得到性能更優(yōu)的零件,組織更加均勻,但成形精度較低,工藝復(fù)雜,應(yīng)考慮工藝改進(jìn)或者實(shí)施相應(yīng)的后處理工藝。增材制造硬質(zhì)合金的一個主要應(yīng)用是生產(chǎn)刀具和模具,因此,相應(yīng)零件的切削耐久性、斷裂行為、磨損機(jī)理應(yīng)進(jìn)一步研究。為了擴(kuò)展增材制造硬質(zhì)合金零件的適用性,未來研究中應(yīng)結(jié)合傳統(tǒng)工藝如熱等靜壓,進(jìn)一步提高零件的綜合性能,滿足復(fù)雜零件的制備要求。