相關(guān)內(nèi)容
-
一文了解硬質(zhì)合金相關(guān)術(shù)語
1.硬質(zhì)合金指由難熔金屬碳化物和金屬粘合劑組成的燒結(jié)復(fù)合材料,在目前所使用的金屬碳化物中,碳化鎢(WC),碳化鈦(TiC),碳化鉭(TaC)和碳化鈮(NbC)是最常見的成分。鈷金屬作為粘結(jié)劑,廣泛應(yīng)用于硬質(zhì)合金生產(chǎn)中;其它的金屬粘結(jié)劑也可應(yīng)用,如:鎳(Ni),鐵(Fe)等,針對某些的特殊用途,也被采用。
-
高頻疲勞測試,不是所有的金屬材料都適合,為什么?
金屬材料疲勞試驗是指在一定條件下,對金屬材料施加交變載荷或者循環(huán)載荷,以評價其在循環(huán)應(yīng)力下的耐久性和抗疲勞性能。主要有應(yīng)力疲勞和應(yīng)變疲勞,應(yīng)力疲勞通常對應(yīng)高周疲勞,而應(yīng)應(yīng)變疲勞通常對應(yīng)低周疲勞。低周疲勞通常指10的四次方以下的疲勞,高周疲勞通常指10的四次方以上的疲勞,關(guān)于低周疲勞和高周疲勞的界限不是物理上的,是領(lǐng)域內(nèi)的習(xí)慣性或經(jīng)驗性定義。金屬材料的疲勞試驗的主要目的是確定材料的疲勞極限、疲勞壽命以及疲勞裂紋擴展速率,從而幫助預(yù)測材料在長期使用中的壽命和安全性。
-
金屬粉末是什么,有什么用
金屬粉末是一組可以通過還原、熱解、電解等方法制備的相對較小的金屬顆粒。
不同霧化壓力下GH3536 合金粉末制備和氣霧化過程模擬
摘 要 使用真空感應(yīng)熔煉氣體霧化方法,在不同霧化壓力(7、8、9 MPa)下制備了球形GH3536 合金粉末。通過使用多相流模型和離散相模型對噴嘴下方區(qū)域進行了數(shù)值模擬,再現(xiàn)了不同霧化氣壓下的一次霧化和二次霧化過程。實驗和模擬的結(jié)果表明:回流區(qū)的氣體速度和滯止壓力隨霧化氣壓的提高而增加,霧化氣壓的增加使粉末粒度不斷減小,模擬結(jié)果與實驗結(jié)果吻合,驗證了霧化模型的可靠性。提高霧化氣壓可提高細粉收得率,但顆粒尺寸的減小和顆粒形貌的改變會對粉末的流動性能造成直接影響,在霧化壓力8 MPa 下制備的粉末具有最佳的流動性和松裝密度,分別為14.34 (s·50g-1)和4.728 g·cm-3。
關(guān)鍵詞 高溫合金粉末;氣體霧化;霧化壓力;數(shù)值模擬;粒度分布
高溫合金由于其優(yōu)異的抗熱腐蝕性、抗氧化性、高溫穩(wěn)定性和結(jié)構(gòu)穩(wěn)定性,被廣泛應(yīng)用于航空航天、船舶工程和特殊環(huán)境領(lǐng)域[1-2]。隨著高溫合金零部件結(jié)構(gòu)復(fù)雜化和精密化程度的不斷提高,傳統(tǒng)鑄鍛工藝成本高、工期長和質(zhì)量穩(wěn)定性差的缺點日顯突出,嚴重制約了高溫合金零部件的高質(zhì)高效制備。近年來,增材制造技術(shù)的快速發(fā)展為復(fù)雜零部件的高精度制備成形提供了一種全新的選擇。增材制造技術(shù)集設(shè)計與制造于一體,能在實現(xiàn)零部件快速復(fù)雜成形的同時能獲得良好的力學(xué)性能[3–6]。作為增材制造的基礎(chǔ)原材料,球形粉末的球形度、流動性和粒度分布等特性會顯著影響成形試件的微觀結(jié)構(gòu)和力學(xué)性能。因此生產(chǎn)具有理想特性的金屬粉末對于增材制造的發(fā)展至關(guān)重要[7-8]。
氣霧化(gas atomization,GA)具有生產(chǎn)效率高、粉末球形度好和冷卻速度快等優(yōu)良特性,成為制備球形高溫合金粉末的主要方法[9]。在氣霧化過程中,高速的霧化氣體將高溫熔體液流沖擊破碎成小尺寸金屬液滴,然后液滴在霧化室中快速冷卻凝固成球形顆粒[10-12]。以往的研究將整個霧化過程分為一次霧化和二次霧化,一次霧化是指噴射的高速氣體和熔體液流之間的交互作用,導(dǎo)致液柱剝落并形成初始熔滴;二次霧化是將大尺寸初始熔滴分散破碎成為小尺寸液滴的過程[11]。
氣霧化過程通常具有復(fù)雜、快速和劇烈的特點。霧化過程中的熔融態(tài)合金液滴尺寸小并有大量不規(guī)則變形,霧化過程發(fā)生在封閉空間內(nèi)并且一次霧化和二次霧化幾乎同時發(fā)生。因此,常規(guī)的實驗手段難以得到有效的數(shù)據(jù),通過計算流體力學(xué)(computational fluid dynamics,CFD)進行數(shù)值模擬已成為研究霧化特性的重要方法[13–15]。Thompson 等[16]使用離散型模型(discrete phase model,DPM)研究霧化壓力對粉末粒度的影響。研究發(fā)現(xiàn),隨著氣體壓力的增加,粉末的粒度出現(xiàn)不斷減小的趨勢。Zhao 等[17]比較了兩種不同湍流模型下噴射角度對流場和一次破碎過程的影響,結(jié)果發(fā)現(xiàn)雷諾應(yīng)力模型(Reynolds stress model,RSM)能夠比k-ε 模型更準確地模擬流場結(jié)構(gòu)。Zeoli 和Gu[11]研究了高壓氣體對熔體破碎和粒度分布的影響。結(jié)果發(fā)現(xiàn),氣體流場由許多振動波組成,較高的霧化氣體壓力可以提高氣體–熔體表面能轉(zhuǎn)換效率,從而實現(xiàn)更高效的破碎效率。Aydin 和Unal[18]使用數(shù)值模擬研究了不同壓力對氣體速度的影響。結(jié)果表明,隨著霧化壓力的增加,氣體速度不會單調(diào)增加,當壓力為2.7 MPa 時,最大氣體速度為663 m·s-1。Kim 等[19]基于氣霧化數(shù)值模擬結(jié)果優(yōu)化了噴嘴,改善了噴嘴出口區(qū)域的氣體流動行為,從而提高了細粉的產(chǎn)量。Shi 等[20]使用離散型模型研究了閉渦條件下霧化壓力對鐵基非晶合金粉末粒度的影響,數(shù)值模擬結(jié)果與實驗結(jié)果基本一致。
目前,針對氣霧化參數(shù)對粉體影響的研究主要在全粒徑段分布,但對選區(qū)激光熔化成形(selective laser melting,SLM)用18~53 μm 這一粒徑區(qū)間的氣霧化高溫合金粉末制備的相關(guān)研究較少,而合金粉末特性對選區(qū)激光熔化成形試件的質(zhì)量具有直接影響。本文使用真空感應(yīng)熔煉氣體霧化(vacuum induction-melting gas atomization,VIGA)方法在不同霧化氣壓(7、8、9 MPa)下制備高溫合金粉末,并以氣體、熔體和顆粒為研究對象,采用計算流體力學(xué)的手段模擬氣霧化制粉過程中的不同霧化階段,研究霧化氣體壓力對流場結(jié)構(gòu)、霧化過程和粉末粒度的影響,結(jié)合制粉結(jié)果分析霧化氣壓對粉末粒徑分布和粉末特性的影響規(guī)律,從而對選區(qū)激光熔化用高質(zhì)量球形高溫合金粉末氣霧化制備過程中霧化氣壓的選擇提供優(yōu)化和參考,以獲得能提供良好打印性能的優(yōu)良球形合金粉末。
1 實驗和模擬方法
1.1 粉末制備
制粉實驗使用了中國科學(xué)院金屬研究所自主研發(fā)的真空感應(yīng)熔煉氣體霧化設(shè)備,如圖1 所示。粉末制備實驗選用GH3536 合金錠作為霧化原料,采用氬氣為惰性霧化氣體,使用3.5 mm 內(nèi)徑的導(dǎo)流管和40 kW 的熔煉功率,通過改變霧化氣體壓力研究其對GH3536 合金粉末霧化效率、粒徑分布、表面形貌和流動性以及松裝密度的影響,霧化氣壓分別設(shè)置為7、8 和9 MPa。在合金熔化之前,使用真空泵組將壓力降低,有助于在真空感應(yīng)熔煉工藝中保證合金成分的純凈度。合金熔化完全后經(jīng)由熔煉室坩堝下方的導(dǎo)流管進入到霧化室內(nèi),被高速霧化氣流破碎為合金粉末。粉末制備完成后,對高溫合金粉末進行篩分,以獲得18~53 μm 粒度區(qū)間的合金粉末。使用BetterSize2600 激光粒度分析儀測量粉體粒度分布,采用掃描電子顯微鏡觀察不同霧化氣壓下粉末的表面形貌,并通過霍爾流速計測量粉末的流動性和松裝密度。計量50 g 粉末從漏斗口完全流出的時間結(jié)果作為粉體的流動性(s·50g-1),稱量在重力作用下通過漏斗自然堆積狀態(tài)下填平量杯的粉體重量,粉末的松裝密度為量杯內(nèi)粉末質(zhì)量與量杯容積的比值(g·cm-3)。
圖1 真空感應(yīng)熔煉氣體霧化設(shè)備
Fig.1 VIGA equipment
1.2 數(shù)值模擬條件設(shè)置
使用Ansys Fluent 軟件進行建模和計算。氣霧化設(shè)備的霧化罐體積通常很大,龐大的模型會帶來巨大的計算量,因此只選用噴嘴下方50 mm×50 mm的區(qū)域來建立模型進行熔體破碎過程研究,氣霧化區(qū)域的二維模型如圖2 所示。與實際霧化工況不同,建模過程以X 軸作為重力方向和對稱軸,左側(cè)邊界分別設(shè)置速度入口和壓力入口,其余左側(cè)邊界為壁面條件,上邊界和右邊界為壓力出口。高溫合金熔體通過速度入口進入霧化區(qū)域,噴嘴的氣體入口被定義為壓力入口邊界條件,熔體進入霧化室的入口被設(shè)置為速度入口邊界條件,霧化室出口邊界被設(shè)置成壓力出口邊界類型。流場的中心線設(shè)置為對稱軸。壁面邊界設(shè)置為300 K 恒溫,出口壓力設(shè)置為標準大氣壓101 kPa,熔體入口速度為1.8 m·s-1。霧化模擬過程中用到的氬氣和GH3536 合金熔體物性參數(shù)如表1[21]所示。由于氬氣進入到霧化區(qū)域的速度遠高于熔融金屬,在先通入氣體的情況下,熔融金屬下落時容易造成金屬熔體的“反噴”現(xiàn)象,從而導(dǎo)致霧化過程停止。因此,當使用流體體積(volume of fluid,VOF)多相流模型用于一次霧化模擬時,根據(jù)實際工藝操作,首先將金屬熔體落入霧化位置,然后再引入高速氬氣以破碎高溫合金熔體。
表1 真空感應(yīng)熔煉氣體霧化過程模擬中氬氣和GH3536 合金物理性質(zhì)[21]
Table 1 Physical properties of the argon and GH3536 superalloys in VIGA process simulation[21]
圖2 氣霧化區(qū)域二維模型
Fig.2 Two-dimensional model of the gas atomization region
2 結(jié)果和討論
2.1 單相氣體流場結(jié)構(gòu)的數(shù)值模擬
圖3 顯示了霧化區(qū)域內(nèi)單相氣體流場的速度分布。當霧化氣體在高壓下通過噴嘴進入霧化室時,由于壓力差,在噴嘴出口處形成膨脹波。氣流膨脹后,速度增加,壓力降低,形成超音速氣流(>340 m·s-1),最大流速可達514 m·s-1。圖3(b)顯示了流場內(nèi)的速度方向??梢杂^察到,在導(dǎo)流管下方有一個與主射流相反的速度,形成了一個呈倒錐形的回流區(qū)。在錐形的頂點處存在一個速度為0的點,被稱為滯點,滯點上方和下方的氣流呈現(xiàn)出完全相反的運動方向。從噴嘴出口進入霧化室內(nèi)的氣體相交于滯點下方,會導(dǎo)致靠近導(dǎo)流管底部位置的部分氣體改變流動方向進入回流區(qū)內(nèi),回流區(qū)內(nèi)的氣體沿軸向自下而上運動到導(dǎo)流管底部后改變方向,沿徑向離開回流區(qū)重新匯聚到主射流邊緣。以往的研究表明,通過導(dǎo)流管進入霧化室內(nèi)的合金熔體首先與回流氣體接觸,并在回流氣體的作用下變形破碎。回流區(qū)的形成是熔體一次霧化的直接動力,因此回流氣體速度將對霧化效率產(chǎn)生直接影響。
圖3 單相氣體流場速度分布(a)和流場內(nèi)速度方向(b)
Fig.3 Velocity distribution of the single-phase gas vector field (a) and the velocity direction in the vector field (b)
不同霧化氣體壓力下,霧化區(qū)域內(nèi)單相氣體流場軸線上的速度如圖4 所示。從速度曲線可以看出,在不同壓力下均形成了明顯的氣體回流區(qū)。從導(dǎo)管末端開始,氣流沿軸向加速,當?shù)竭_回流區(qū)中心位置時速度達到最大??梢钥闯觯S著霧化壓力的增加,回流氣體的最大速度也呈現(xiàn)不斷增加的趨勢,在9 MPa 的霧化壓力下,回流區(qū)的最大速度達到237 m·s-1(I),金屬熔體在回流區(qū)內(nèi)與回流氣體接觸發(fā)生變形破碎,更大的氣流速度更有利于一次霧化的進行。隨后氣體速度不斷減小,并且在滯點處氣體速度降低至0(II),經(jīng)過滯點后,氣流速度方向發(fā)生改變并加速至一段距離后穩(wěn)定在270~350 m·s-1 之間(III)。
圖4 不同霧化壓力下的速度曲線
Fig.4 Velocity curves at the different atomization pressures
不同霧化氣體壓力下,單相氣體流場軸線上的壓力分布如圖5 所示??梢钥闯觯谶h離導(dǎo)流管的方向上,靜壓先逐漸減小后逐漸增大。在回流區(qū)末端滯點附近的壓力非常大,稱為滯止壓力。滯止壓力反映了通過滯點進入到回流區(qū)內(nèi)的氣體流量大小,這也是形成回流區(qū)的必要條件,當滯點處存在壓力差時,滯點上方和下方的氣流將具有相反的速度方向[22]。當霧化壓力提高時,滯止壓力也會增加,霧化壓力為9 MPa 時,滯止壓力為357 kPa。在滯點下方的區(qū)域,出口附近的壓力波動也隨著氣體壓力的增加而增加,這是由于霧化區(qū)域和出口邊界處存在壓力差,壓力波動幅度隨著軸向距離的增加而不斷減小至標準氣壓附近。這種振幅的壓力波動將導(dǎo)致氣流不穩(wěn)定,并容易導(dǎo)致霧化粉末與未完全固化的液滴結(jié)合形成衛(wèi)星粉末,從而影響粉末的質(zhì)量。
圖5 不同霧化壓力下霧化流場中心線上壓力變化曲線
Fig.5 Static pressure curves at the different atomization pressures
2.2 一次霧化過程的數(shù)值模擬
使用VOF 多相流模型進行一次霧化的模擬,在霧化模擬過程中,先通入金屬熔體,當熔體到達導(dǎo)流管底部時通入高速氣體。圖6 顯示了一次霧化過程中高溫合金熔體的不同霧化階段。圖6(a)顯示熔體在重力作用下通過導(dǎo)流管進入霧化區(qū)域。當熔體開始接觸回流區(qū)中的氣流時,熔體的向下流動受到阻礙,并且熔體的流速逐漸減小甚至停止。短暫的相互作用后,熔體在氣流擾動作用下開始沿徑向變形,如圖6(b)所示。隨著回流氣體的不斷擾動,液流兩端開始出現(xiàn)橫向膨脹的液膜,液膜連續(xù)變形并被不斷拉長。最終在回流氣體的作用下導(dǎo)致液膜兩側(cè)的熔體剝落,熔體原有的連續(xù)流動被破壞,形成圖6(d)中的大尺寸熔體液滴。由于大液滴具有相對較小的重量,因此一次霧化產(chǎn)生的大尺寸熔滴將被回流區(qū)中的氣體拖曳至亞音速邊界,以進一步破碎分散形成更小尺寸的液滴。
圖6 一次霧化過程的不同破碎階段
Fig.6 Different stages of the primary atomization simulation
不同霧化壓力下一次霧化破碎后的大尺寸熔滴形狀如圖7 所示。使用Image-Pro Plus 圖像處理軟件計算出大尺寸熔滴的面積,7、8 和9 MPa 霧化氣壓對應(yīng)的液滴面積分別為487688.27、362100.75和237582.94 μm2。隨霧化氣壓的不斷增加,氣流速度和滯止壓強都呈現(xiàn)出升高的趨勢,因此霧化氣體對熔體的霧化破碎效果也會逐漸增強,在霧化過程中氣體動能轉(zhuǎn)化為液滴表面能的效率也隨之增加。將液滴面積計算為熔滴直徑,三個霧化氣壓下的大尺寸熔滴粒徑直徑分別為788、679 和550 μm,呈現(xiàn)出隨霧化氣壓的增大而不斷減小的趨勢。一次霧化產(chǎn)生的熔滴由于其尺寸較大,在霧化室內(nèi)飛行過程中會由于自身的不穩(wěn)定性和在高速氣流的沖擊作用下發(fā)生二次霧化破碎,形成尺寸更為細小的液滴。二次霧化的數(shù)值模擬計算以一次霧化的結(jié)果作為初始條件,所以一次霧化產(chǎn)生的熔滴尺寸會對最終的粒徑分布產(chǎn)生直接影響。
圖7 一次霧化過程中不同霧化氣壓下熔滴尺寸:(a)7 MPa;(b)8 MPa;(c)9 MPa
Fig.7 Droplet size at the different atomization pressures during the primary atomization simulation: (a) 7 MPa; (b) 8 MPa; (c) 9 MPa
2.3 二次霧化過程的數(shù)值模擬
二次霧化也被稱為二次破碎,是指在一次霧化后形成的較大尺寸的液滴或液片在高速氣流作用下由于自身的不穩(wěn)定性再次霧化破碎,形成較小尺寸液滴的過程。為了近似真空感應(yīng)熔煉氣體霧化過程制備高溫合金粉末的二次霧化過程和粉末粒度分布,基于一次霧化的模擬結(jié)果,選用Fluent 中的離散型模型對高溫熔體進行二次霧化過程的數(shù)值模擬。
使用Fluent 軟件的顆粒追蹤功能,將一次霧化液滴屬性加載到離散型模型中進行二次霧化的數(shù)值模擬。首先通入霧化氣體獲得穩(wěn)定的單相氣體流場,然后在流場中加載一次霧化產(chǎn)生的大尺寸液滴,二次霧化過程中金屬液滴的顆粒尺寸變化過程和飛行軌跡可在圖8 中完整顯示??梢钥闯觯淮戊F化產(chǎn)生的大尺寸液滴在回流氣體和自身重力的作用下徑向移動。二次破碎過程主要發(fā)生在氣體噴嘴出口下方,這主要是由于回流區(qū)內(nèi)的氣體動能較小,不足以使熔滴發(fā)生破碎,而噴嘴下方的氣體速度較快從而提供了更多的破碎能量。最終,破碎完成顆粒在氣體的作用下離開霧化室??梢钥闯觯暾念w粒軌跡與一次霧化的單相氣流結(jié)構(gòu)基本一致。
圖8 二次霧化過程中液滴的不同破碎階段
Fig.8 Different stages of the second atomization simulation
通過Fluent 軟件監(jiān)測物理模型的出口邊界,計算顆粒信息,并獲得第二次霧化后粒徑在18~53 μm 之間的液滴粒徑尺寸分布,如圖9 所示。當霧化壓力為7 MPa 時,由于提供破碎的霧化氣體動能較低,霧化后獲得的顆粒尺寸集中分布在39~49 μm,粉末的中值粒度D50 為42.35 μm,粉體尺寸整體較大。提高霧化壓力至8 MPa,霧化后的粒度集中在32~46 μm 范圍內(nèi),粉末中值粒度D50 為38.36 μm。當霧化壓力為9 MPa 時,粉末的粒徑集中在28~39 μm 的范圍內(nèi),粉末的中值粒徑D50 為34.88 μm。隨著霧化壓力的增加,回流區(qū)內(nèi)的氣體流量和氣流速度增加,從而提供了更多的霧化動能,進而提高了破碎效率。因此,粉末的粒度尺寸呈現(xiàn)出不斷減小的趨勢。
圖9 二次霧化后的顆粒尺寸分布:(a)7 MPa;(b)8 MPa;(c)9 MPa;(d)累積分布曲線
Fig.9 Particle size distribution obtained by the secondary atomization simulation: (a) 7 MPa; (b) 8 MPa; (c) 9 MPa; (d) cumulative distribution curves
2.4 粉末特性
圖10 顯示了不同壓力下真空感應(yīng)熔煉氣體霧化法制備的GH3536 合金粉末的掃描電子顯微形貌??梢钥吹? MPa 霧化氣壓下粉末顆粒的尺寸較大,粉末表面光潔程度較高,衛(wèi)星粉末和粘結(jié)情況較少。隨著霧化壓力的增加,粉末的尺寸出現(xiàn)了不斷減小的趨勢,小尺寸粉末的數(shù)量不斷增加,并且粉末的球形度變差,衛(wèi)星粉末的數(shù)量也隨之增加。這是由于較大的霧化壓力提供了更大的霧化所需動能,因此產(chǎn)生了更多微細尺寸顆粒,在霧化過程完成后,熔滴在霧化室內(nèi)完成冷卻凝固形成球形顆粒,但小尺寸熔滴的冷卻速度快,在飛行過程中由于不同尺寸的熔滴速度不同,導(dǎo)致粉末之間發(fā)生碰撞,從而形成更多的衛(wèi)星粉末和不規(guī)則粉末,導(dǎo)致粉體的球形度降低。因此,在8 MPa 和9 MPa 霧化氣壓下制備的粉末中出現(xiàn)了更多的不規(guī)則粉末和衛(wèi)星粉末。隨霧化氣壓的升高,粉末粒徑尺寸減小,粒徑尺寸在15~53 μm 范圍內(nèi)的微細粉末收得率不斷增加。
圖10 不同霧化氣壓下真空感應(yīng)熔煉氣體霧化法制備GH3536 顆粒掃描電子顯微形貌:(a)7 MPa;(b)8 MPa;(c)9 MPa
Fig.10 SEM images of the GH3536 alloy powders prepared by VIGA at the different atomization pressures: (a) 7 MPa; (b) 8 MPa;(c) 9 MPa
圖11 是在不同霧化壓力下制備的GH3536 粉末粒徑分布。從圖中可以看出,當霧化壓力為7 MPa時,粉末粒徑集中分布在41~49 μm 之間;當霧化壓力為8 MPa 時,粉末粒徑集中分布在36~49 μm;當霧化壓力提高到9 MPa 時,粉末直徑集中分布在28 至43 μm 范圍內(nèi)。由圖11(d)可知,隨著霧化壓力的增加,粉末的累積粒徑分布曲線左移,中值粒徑D50 分別為41.48、36.88 和32.63 μm。由于霧化壓力增加,氣體的速度和動能增加,因此對熔融金屬的破碎效率更高,粉體顆粒的尺寸集中分布在更小的粒徑區(qū)間內(nèi)。表2 為不同霧化氣壓下數(shù)值模擬和制粉實驗得到的粉末中值粒徑的對比,可以看到隨霧化氣壓的增加,粉末顆粒的中值粒徑都呈現(xiàn)出不斷減小的趨勢,這說明霧化氣壓的提高導(dǎo)致了霧化動能的增加,從而提高了熔體的破碎效率,因此二次霧化后的粉末尺寸不斷減小,數(shù)值模擬和實驗結(jié)果都呈現(xiàn)出了相同的變化趨勢,并且數(shù)值模擬的誤差較小,驗證了氣霧化流場數(shù)值模擬模型的可靠性。
表2 不同霧化氣壓下真空感應(yīng)熔煉氣體霧化制備粉末和數(shù)值模擬粉末中位粒徑
Table 2 Experimental and simulation data of the median particle size for the GH3536 superalloy powders by VIGA
圖11 不同霧化氣壓下粉末粒徑分布:(a)7 MPa;(b)8 MPa;(c)9 MPa;(d)累積分布曲線
Fig.11 Particle size distribution at the different atomization pressures: (a) 7 MPa; (b) 8 MPa; (c) 9 MPa; (d) cumulative distribution curves
圖12 顯示了在不同霧化壓力下制備的GH3536合金粉末流動性和松裝密度。隨著霧化氣壓的增加,粉末的流動時間先降低然后增加。這是因為粉末的粒度隨著壓力的增加而減小,在測試流動性過程中每單位時間通過漏斗的粉末的數(shù)量增加,因此粉末流動速度加快。然而,在9 MPa 的壓力下,破碎粉末和衛(wèi)星粉末數(shù)量的增加導(dǎo)致粉末的球形度降低,導(dǎo)致單位時間內(nèi)通過漏斗的粉末數(shù)量減少,因此粉末的流動性出現(xiàn)了退化現(xiàn)象;隨著霧化壓力的增加,粉末的粒度減小,粉末的間隙變小,因此具有更好的松裝密度。在9 MPa 的霧化壓力下,由于不規(guī)則粉末和衛(wèi)星粉末數(shù)量的增加,在粉末依靠重力自然堆積的情況下,會產(chǎn)生更多的“架橋”現(xiàn)象,因此造成了自然堆積狀態(tài)下空隙的增加,從而導(dǎo)致了松裝密度出現(xiàn)了先增加后減少的情況。在8 MPa壓力下,粉末具有最佳的流動性和松裝密度,流動性為14.34 (s·50g-1),松裝密度為4.728 g·cm-3。
圖12 不同霧化氣壓下GH3536 粉末流動性和松裝密度
Fig.12 Flowability and apparent density of the GH3536 powders at the different atomization pressures
3 結(jié)論
(1)結(jié)合多相流和離散型模型,再現(xiàn)了GH3536高溫合金的一次和二次霧化過程:金屬熔體在導(dǎo)流管下方的回流區(qū)內(nèi)發(fā)生形變破碎并形成初始熔滴,完成一次霧化;隨后初始熔滴在氣體噴嘴出口下方的高速氣流作用下完成了二次霧化破碎。
(2)隨著霧化壓力的提升,回流區(qū)的氣體速度和滯止壓力逐漸增加,從而提高了霧化破碎效率,細粉收得率隨霧化氣壓的增加出現(xiàn)了不斷提高的趨勢,粉末粒徑集中分布在更小的粒徑區(qū)間內(nèi),實驗制得粉末中值粒徑D50 從41.48 μm 減小到36.88 μm、32.63 μm,數(shù)值模擬得到的粉末中值粒徑D50從42.53 μm 減小到38.36 μm、34.88 μm,數(shù)值模擬和實驗結(jié)果呈現(xiàn)相同的趨勢,驗證了氣霧化數(shù)值模擬模型的合理性。
(3)當霧化壓力為7 MPa 時,霧化制備的合金粉末具有較好的球形度和表面光潔度。隨著氣體壓力的增加,粉末的粒度和形貌的改變,粉末的流動性能和松裝密度都呈現(xiàn)出先提高后下降的趨勢。當霧化壓力為8 MPa 時,粉末具有最佳的流動性和松裝密度,分別為14.34 (s·50g-1)和4.728 g·cm-3。
文章引用:侯維強, 吳佳欣, 孟杰等. 不同霧化壓力下GH3536 合金粉末制備和氣霧化過程模擬[J]. 粉末冶金技術(shù), 2023, 41(5): 410-419.
聲 明:文章內(nèi)容來源于材料成型及模擬分析。僅作分享,不代表本號立場,如有侵權(quán),請聯(lián)系小編刪除,謝謝!
關(guān)注官微
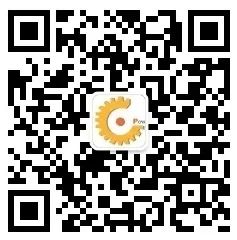
加入群聊
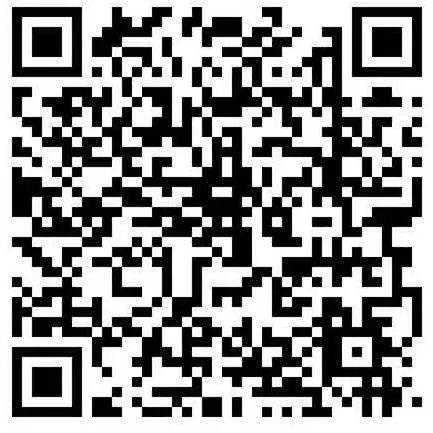